Fly News ha visitado la factoría de Airbus Helicopters en Albacete para conocer de cerca los trabajos que allí se efectúan dentro del programa NH90.
Con motivo del primer vuelo de un helicóptero NH90 para la Armada española, hemos visitado Airbus Helicopters en Albacete, donde se fabrican los fuselajes completos de este modelo para su entrega a clientes de todo el mundo.
La producción de los NH90 se lleva a cabo en cuatro factorías: Albacete, donde se fabrican las dos secciones que forman el fuselaje: Morro, y central y se ensamblan junto al fuselaje posterior; y Marsella (Francia), Donauworth (Alemania), y Venecia (Italia) donde están las cadenas de montaje final. La italiana es solo para los helicópteros de ese país.
En nuestra visita fue Aina Monfort, directora de operaciones de Airbus Helicopters en España y directora de la planta de Albacete, quien nos mostró las instalaciones.
Los primeros NH90 de FAMET se montaron en Albacete, pero en 2014 Airbus Helicopters decidió hacer cambios en sus sistemas productivos, lo que llevó al cierre de las cadenas de montaje españolas, y su especialización en fuselajes traseros para todos los helicópteros, y en los fuselajes del NH90.
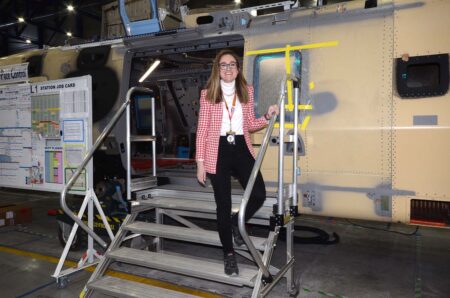
La pérdida de las cadenas de montaje en Albacete, en contra de lo que pueda parecer, fue una buena noticia. Para Aina Monfort este cambio fue muy interesante, ya que: “Lo que hacemos es parte del helicóptero, pero para todos los helicópteros que se entregan. Es más carga de trabajo, y es más estable, porque al final no dependes únicamente de los pedidos que España. Al final España es una contribuidora, nosotros por supuesto hacemos los elementos españoles, pero también hacemos los de los demás clientes. Con lo cual a la hora de la estabilidad de la planta, de la estabilidad de los equipos, es mucho mejor”.
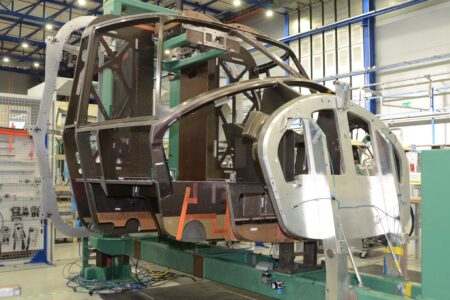
En este sentido, nos explica que en al inicio de 2023 ha concluido la transferencia de la producción de los fuselajes centrales de Alemania a España: “Esto ahora nos da una ventaja, porque antes este elemento era uno que te venía hecho de fuera, pero ahora mismo nos da visibilidad de todo el proceso de principio a fin, y eso nos va a permitir mejorar a nivel de proceso”.
En Albacete la producción del NH90 se divide en dos líneas de trabajo. Una para el fuselaje delantero, básicamente la cabina de los pilotos, y la otra para el fuselaje central. Ambas secciones finalmente se unen entre sí y con el fuselaje trasero. Esta última sección es responsabilidad de Leonardo (Italia) pero está subcontratada con Aernnova que las produce en Sevilla.
Con las tres secciones unidas, el NH90, con parte de sus sistemas, cableado y tuberías ya instalados, se envía por camión a Donauworth en Alemania o Marignane en Francia, donde se terminan los trabajos. La excepción son los helicópteros de cuyo montaje se encarga Leonardo en sus instalaciones en el aeropuerto de Venecia (Italia). Estos son enviados a Italia sin unir entre si las tres secciones, según nos explicó Monfort.
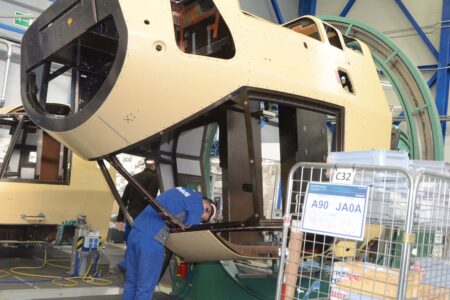
En Albacete, se han reservado dos hangares de las instlaciones para el NH90, con una superficie combinada de más de 4.000 metros cuadrados. En el primero se lleva a cabo la producción de los dos segmentos del fuselaje, y en el segundo la unión de ambos y demás trabajos. Actualmente la cadencia de producción del NH90 es de unos 15 aparatos al año.
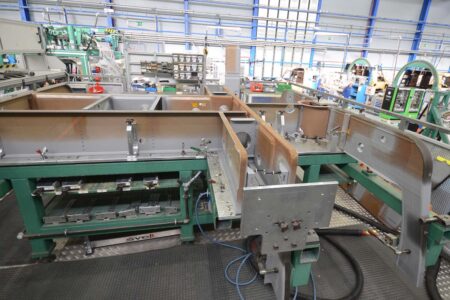
La fabricación de los NH90 en Albacete comienza con la recepción de las piezas elementales que los formarán: Larqueros, costillas, paneles… Estas son producidas por varios subcontratistas españoles.
De hecho son una docena las empresas españolas que participan en el programa. El 80 por ciento de las piezas elementales del fuselaje delantero las produce Internacional de Composites SA (ICSA, una división de Aernnova) en Toledo. El 15 por ciento llega de Airbus Helicopters en Alemania, y el 5 por ciento restante de proveedores externos.
En el caso del fuselaje frontal, son nueve las estaciones de trabajo en que se divide la producción. La primera pieza que se completa es el marco del parabrisas, el cual llega en dos partes.
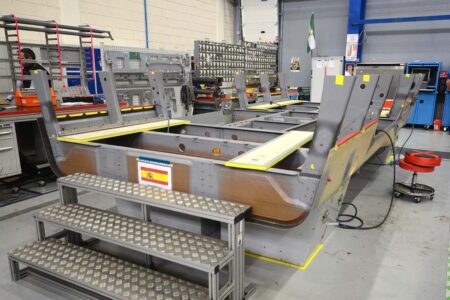
La estructura del suelo es lo primero que se monta tras ese marco. En paralelo se van formando otras zonas que después se van uniendo entre ellas, y posteriormente las pieles, los paneles que forman la estructura exterior del fuselaje. Para la unión de todos estos componentes se usa un pegamento estructural que se activa mediante calor en un horno. “Una pieza puede pasar como máximo cuatro veces en el horno”, nos detalla Aina Monfort. También se montan algunos componentes internos por la mayor facilidad para hacerlo en este momento.
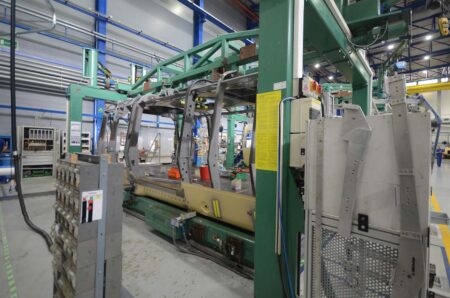
La sección pasa por una máquina de control numérico donde se inicia ese proceso mediante el taladro de los agujeros precisos para la instalación de los equipos de cada cliente pero también sistemas generales: “Metemos provisiones de antenas, bandejas, fittings, cableado, tuberías, todo lo que podemos adelantar equipando en la evolución que va cogiendo el helicóptero”.
En el caso del fuselaje central, son una docena las estaciones de trabajo. El montaje comienza también por el suelo de la cabina, uniendo sus largueros y cuadernas que han llegado, junto a las pieles, desde Airbus Helicopters en Alemania en su mayoría. En paralelo se va dando forma a la mitad superior de la cabina. Una vez completadas las dos, y con determinados elementos ya instalados, como en la sección de morro, por ser más sencillo hacerlo en este momento que posteriormente, las dos mitades se envían al segundo hangar donde se procede a su unión y posteriormente con el fuselaje delantero y el trasero.
Antes de este paso, también se taladran los agujeros por ejemplo para el anclaje de las antenas exteriores y para su cableado.
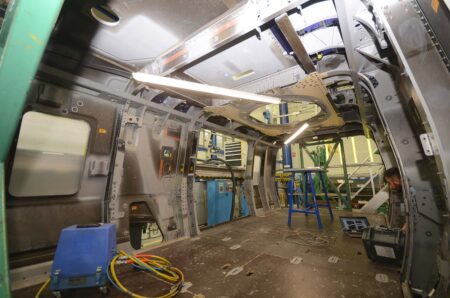
Todo lo que va bajo el suelo de la cabina de carga/pasaje queda instalado en Albacete y cerrado. Toda esa zona queda ya completamente terminada y no habrá que tocar nada allí salvo que se detecte algún problema durante las fases posteriores.
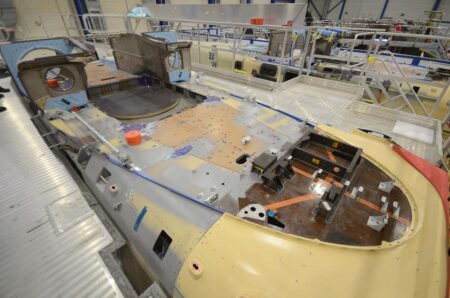
La unión de las tres secciones se lleva a cabo mediante sistemas láser de medición que aseguran que el eje de transmisión al rotor trasero está perfectamente alineado y en su sitio. Con esta pieza, que tiene una tolerancia cero, así calibrada, las otras secciones quedan automáticamente alineadas.
Las uniones entre las tres secciones del fuselaje se refuerzan con un remachado que se suma al sistema de pegado que es el principal medio de unión. Según nos aclara Aina Monfort, el sistema de pegado usado permitiría resistir sin romperse las cargas que el helicóptero sufrirá a lo largo de su vida operativa “pero se le pone un extra para reforzar esas áreas tan críticas”.
Una vez unidas se terminande instalar elementos que hasta ese momento no tenía sentido haberlo hecho. Aina Monfort nos pone como ejemplo un cable que pueda ir desde la parte delantera a la trasera. Así se instala un solo cable de una vez en lugar de secciones que haya que unir.
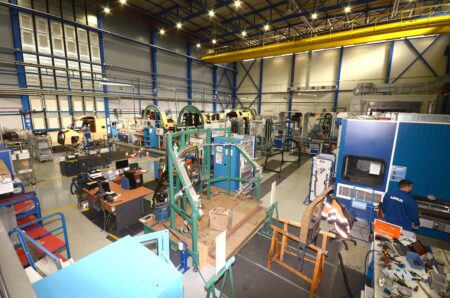
Ya con las secciones unidas, se realiza la llamada prueba de lluvia. Que no es otra cosa que comprobar la estanqueidad de la célula ante el agua. Una vez el helicóptero reciba todos los demás componentes en las cadenas de montaje final, esta prueba se repetirá.
El transporte de las células completas a Alemania o Francia, así como las secciones si unir destinadas a Italia se realiza en camión.
La producción de las secciones del NH90 y su ensamblaje en Albacete consumen unas 7.000 horas de trabajo. El fuselaje frontal requiere unos 130 días de trabajo, mientras que el central unos 100.
EL REGRESO A ALBACETE
Una vez que en Alemania (en el caso de los NH90 de la Armada) o en Francia se han completado los denominados vuelos industriales que hemos citado, los NH90 para las fuerzas armadas españolas regresan a Albacete.
Allí se terminan de equipar con los sistemas y equipos de misión españoles y se vuelven a probar en vuelo, tanto por pilotos de Airbus Helicopters, como por pilotos del cliente antes de su entrega oficial a la Dirección General de Armamento y Material del ministerio de Defensa español. La instalación en territorio español de algunos sistemas responde a temas de soberanía nacional, confidencialidad y seguridad.
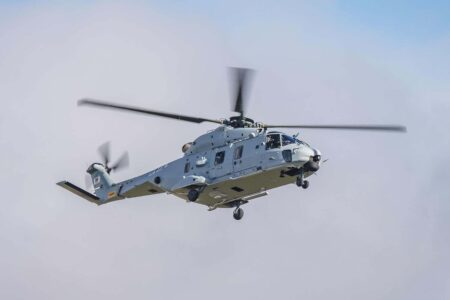
En el caso del NH90 de la Armada, este período en Albacete va a ser algo más largo de lo habitual al ser un cabeza de serie. Con todo, Monfort confía en que se entregue a finales de 2024, y retomar las entregas de unos 8 NH90 al año, después de que en 2023 no hubiese entregas, de acuerdo al calendario del ministerio de Defensa español.
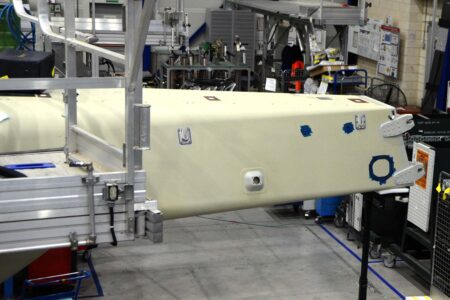
Un punto a destacar es que tanto desde la factoría de Albacete, como por parte del cliente, hay un seguimiento continuo de cada helicóptero tanto en España como en Alemania o Francia: “Nosotros, en todo momento, a los helicópteros españoles les damos seguimiento. Es decir, aunque el helicóptero salga de aquí, no sale y nos olvidamos y solo lo recibimos cuando vuelve. Tenemos a gente que está siguiendo la evolución de ese helicóptero en el proceso de montaje final para entender cómo va, qué problemas se encuentran, que se agiliza como se tiene que agilizar, que se prioriza como se tiene que priorizar. Todo para que a la llegada aquí no sea un helicóptero nuevo, sino un helicóptero que conocemos y que hemos seguido desde el principio”.
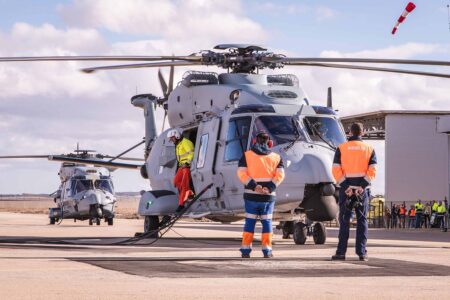
Entre vuelos industriales, certificación y entrega, son algo menos de 20 horas de vuelo (si no hay nada que obligue a repetir algún vuelo), con las que cada aeronave abandona la planta de Airbus Helicopters.
Añadir comentario