Desde la sustitución de bridas de plástico por otras de papel en los mazos de cables, pasando por la utilización de materiales inteligentes en el ala del avión que permiten cambiar la configuración de la misma durante el vuelo, pasando por un simulador virtual o una cabina inteligente, estos son algunos de los «inventos» en los que los trabajadores de Airbus piensan para mantener el liderazgo tecnológico de la industria de la aviación.
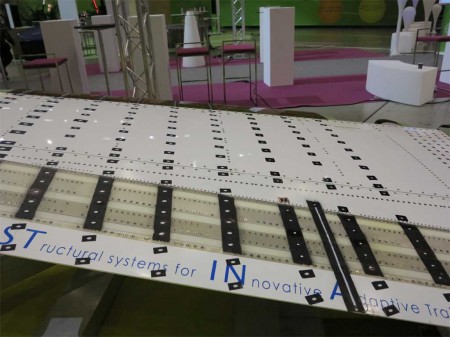
En la factoría de Airbus en Broughton, Reino Unido, los operarios quitan más de 800.000 bridas de plástico al año de los mazos de cables que van en el interior de las alas del A320. La operación, además de incómoda y lenta, es peligrosa para la integridad del cable. El pequeño alicate con el que se cortan puede ocasionar «daños colaterales», además de incrementar considerablemente el tiempo de manipulación del componente. Así, Maud Didnee, una trabajadora de la factoría inglesa, pensó en cómo hacer más fácil esta tediosa tarea. La solución, sustituir el duro y antiecológico plástico por bridas de papel, fáciles de separar, ligeras y más respetuosas con el medio ambiente.
Esta es una de las 6.000 patentes que los empleados de Airbus registran al año, y que van desde aviones con estructuras transparentes, pasando por asientos en forma de litera para aumentar la capacidad de los mismos o el desarrollo de materiales inteligentes que cambian su forma y su configuración dependiendo de las condiciones de vuelo. Todo ello en una estrategia de innovación que va de abajo arriba y de izquierda a derecha, involucrando a toda la organización.
Esto es lo que ha querido mostrar el fabricante europeo a clientes, trabajadores y prensa, en una showroom de la innovación. Para los medios de comunicación eligieron diez proyectos que abarcan casi todas las áreas de actividad de la compañía, muchos de ellos ideados, como el de las bridas de papel, por los operarios de las fábricas del constructor aeronáutico europeo.
Según explicó el director de innovación del fabricante europeo, Yann Barbaux, existen dos grandes tendencias de futuro que cambiarán la manera de producir y de operar las aeronaves, la digitalización, y el IoT, o internet de las cosas. Así, Airbus prepara este futuro, por ejemplo, diseñando un simulador virtual de vuelo. Según Daniel Dreyer, responsable de este proyecto, se trata de utilizar la realidad virtual en una fase previa al «carísimo» diseño de un simulador de cabina de vuelo, que permite, además de incrementar la eficacia en el diseño, una importante reducción de tiempo. El «piloto» virtual prueba el diseño del simulador y va introduciendo las modificaciones precisas en función de características como la ergonomía, accesibilidad, etcétera.
Otro de los proyectos innovadores en este área ensaya el escaneo completo de las estructura del avión para identificar cuáles son las piezas más aptas para producirse por impresión 3D. De los más de seis millones de piezas que tiene un avión, el GEOsearch, que así se llama el invento, es capaz de identificar cientos de miles de componentes susceptibles de ser fabricados en una impresora 3D. Las ventajas, según el responsable del proyecto, Sten Gatzke, la reducción del coste de producción y del tiempo. El GEOSearch ha pasado, además, la frontera de proyecto y el primer dispositivo entró ya en servicio en julio de 2015.
BANCOS DE ENSAYOS VIRTUALES y SMART GLASSES EN LA CADENA DE PRODUCCIÓN
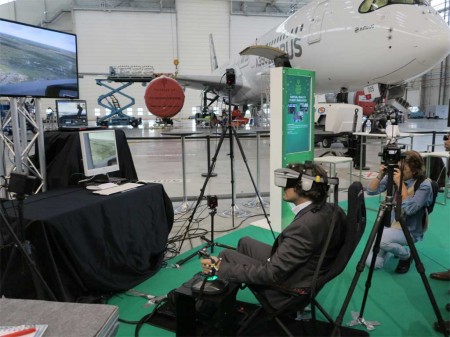
¿Cómo se puede ahorrar tiempo, dinero y espacio en los prolongados ensayos a los que se someten todos los componentes de un avión antes de su instalación en la aeronave? Esto es lo que pensó David Cumer y su equipo, al desarrollar un banco de ensayos virtual en el que se han sutituido todos los cables de un banco convencional. La «buena idea» es que utilizan procesadores que ya existen en el mercado para transmitir la información de las pruebas, el prototipo visto en Toulouse está pensado para pruebas de circuitos hidráulicos.
Otro de los proyectos que ha pasado la fase de prototipo y ya se utiliza en la cadena de producción, son unas smarts glasses que ya utilizan los operarios de la planta de Hamburgo en fase piloto, y que indica al trabajador el lugar exacto donde debe realizar el remache o colocar uno de los cientos de letreros que se instalan en el interior de las cabinas. Como en la mayoría de los proyectos mostrados en Toulouse, se parte de dispositivos que existen en el mercado, o de material básico que se tecnifica utilizando, igualmente, tecnología ya disponible. En este caso, el componente básico son las gafas protectoras que ya utilizan los operarios, a las que se añade una cámara que escanea las órdenes de trabajo de la posición del operario y muestra los parámetros exactos para realizar las distintas tareas con mayor precisión y «a la primera».
En un estadio superior de investigación pura, se enmarca otro proyecto, el desarrollo de Estructura Inteligentes, Saristu, que es una línea de investigación del VII Programa Marco Europeo, con una financiación de 51 millones de euros, 32 de ellos aportados por instituciones públicas, y el resto por la industria, y que ha involucrado hasta 1.500 personas trabajando en algunas de las fases del programa. El objetivo, según explicó Piet Christof Woelcken, es reducir los costes operativos de un avión mediante la utilización de materiales que puedan cambiar de forma en función de las condiciones de vuelo, el control del estado de los materiales de la estructura, todo ello utilizando materiales más avanzados.
En concreto, la investigación que lleva a cabo este equipo de Airbus se ha centrado en el desarrollo de una ala que permite el cambio de configuración en cada momento del vuelo, mediante la utilización de nuevos materiales y de un diseño distinto. En Toulouse vimos como un nuevo diseño de los bordes de salida y ataque del ala permiten adaptarse a estas condiciones específicas. Además, utilizando este diseño en el winglet se reduce considerablemente el consumo. En definitiva, se trata de un ala que cambia su configuración dependiendo de cada momento del vuelo Dentro de este proyecto se investigan nuevos materiales multifuncionales para mejorar, por ejemplo, las propiedades eléctricas y mecánicas o, a el desarrollo de sensores incluidos en estos nuevos materiales que monitoricen de forma más eficaz el estado del componente en todo momento.
También se investiga en Airbus cómo aprovechar el Internet de las Cosas en beneficio de la operación de los aviones. Así, un equipo del fabricante europeo diseña una «cabina inteligente» que mediante un sistema de identificación por radiofrecuencia, Auto ID, permite conectar con los distintos objetos que se instalan en la cabina de un avión, obteniendo información sobre elementos críticos de la cabina, como su estado y su fecha de caducidad.
Actualmente este proyecto se aplica sobre más de 3.000 items en el A3350 equipados con equipos de radiofrecuencia. Desde Airbus explicaron que el sistema en el futuro estará presente en todos los modelos que fabrican, y prevén en el sistema esté listo dentro de dos años.
Añadir comentario