Airbus ha dado por finalizado el montaje estructural del primer A321XLR de los tres que se usarán para la certificación.
El primer Airbus A321XLR, msn11000, ya está estructuralmente terminado en la factoría de Airbus en Finkenwerder (Hamburgo, Alemania), donde volará en 2022 con el objetivo de la certificación y entrada en servicio del modelo en 2023.
A este avión se unirán pronto los msn11058 y msn11080, que serán los otros dos que se usarán para la certificación.
Este primer A321XLR ha sido montado en la segunda línea de montaje (FAL por las siglas en inglés de línea final de montaje) del modelo de las cuatro que hay ya establecidas en la factoría alemana.
ASÍ SE MONTA EL A321
Una vez los principales elementos estructurales llegaron a la FAL, en las estaciones 42 y 43 se preparan las secciones de popa y proa del avión, y se aprovecha para instalar elementos interiores como lavabos y galleys. La sección trasera incluye el nuevo depósito de combustible de 12.900 litros, exclusivo de esta variante, y gracias al cual alcanza los 8.700 km sin escalas. También en la parte inferior de estas secciones se ha instalado un depósito de aguas residuales más grande que el usado en otros A321 como consecuencia de los vuelos más largos que va a realizar.
Desde estas estaciones, ambas secciones fueron trasladadas a la estación 41, donde se unieron con la sección central del fuselaje, con más de 3.000 remaches. En esta estación también se instalan el suelo, el recubrimiento de la cabina de pasaje y los sistemas eléctricos de esta; y el sistema de carga.
Posteriormente, todo el fuselaje es instalado en la estación 40, donde se une a las alas (mediante 2.400 remaches) y se instalan el tren de aterrizaje y los pilones de los motores; y se lleva a cabo el primer encendido eléctrico de los sistemas para sus primeras pruebas. Esto se hace con electricidad suministrada desde el exterior, dado que el avión todavía no cuenta con sus principales generadores eléctricos: los motores y la unidad de potencia auxiliar (APU por sus siglas en inglés).
La siguiente estación es la 35, donde se añade la deriva vertical, los estabilizadores horizontales y el cono de cola, estos dos últimos construidos en España. También se instalan los flaps interiores, las puertas del tren de aterrizaje principal (fabricadas en España), el radomo, el radar meteorológico, los conductos de aire, el sistema de aire acondicionado, el sistema de agua, el sistema de combustible, el carenado ventral (construido también en parte en España), APU y todas las puertas de pasajeros y de carga. En el interior de la cabina de pasaje se instalan los paneles de pared, armarios superiores, y las unidades de servicio del pasajero (que incluyen las luces, salidas de aire personales y pulsador de llamada a la tripulación, máscaras de oxigeno, luces de cinturones, no fumar y no usar dispositivos electrónicos), En las bodegas de carga también se colocan los paneles interiores; y finalmente se sellan los depósitos de combustible de las alas. En esta estación también se llevan a cabo las primeras pruebas del sistema hidráulico.
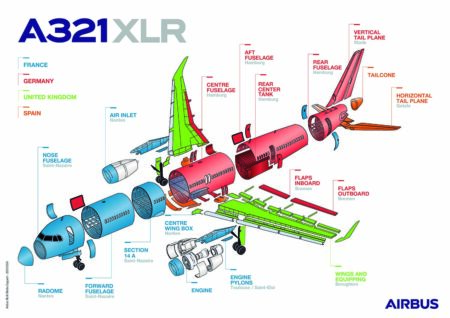
Y de esta estación se pasa a la 25, donde se encuentra actualmente el avión, para completar la instalación de la cabina de pasaje y la prueba de sus elementos, del sistema de presurización, aviónica —incluyendo radios y equipos de navegación—, y de combustible para comprobar que no hay fugas.
Una vez completadas estas pruebas se instalarán los motores, para volver efectuarlas con energía procedente de estos, y se instalarán los últimos elementos como carenados no estructurales y se harán pruebas de vibración para asegurarse que todo está bien sujeto en su sitio y no se va a caer nada durante el vuelo.
Superadas todas estas pruebas, el avión pasará al departamento de vuelo, donde llevarán a cabo una nueva tanda de ensayos antes del primer vuelo.
Añadir comentario